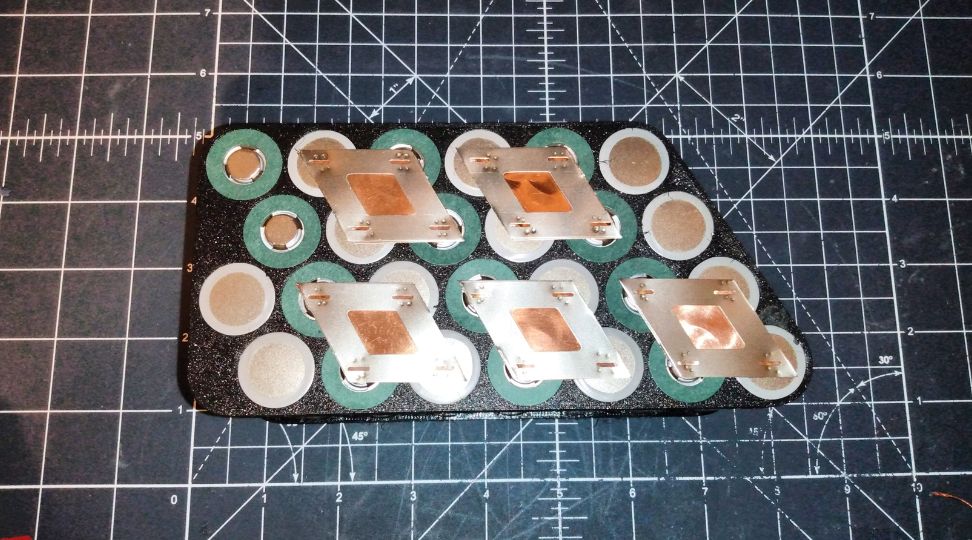
Why Do You Use Nickel Strips For Battery Packs
Table of Contents
When it comes to constructing battery packs, material selection is super important for optimizing performance, longevity, and safety. Out of all the materials available, nickel is the primary material used to make battery packs. So, why do you use nickel strips for battery packs?
Nickel strips are used in battery packs because they are thermally stable, they have a high degree of corrosion resistance. Nickel strips also have a high tensile strength and ductility, and it’s cheap.
Nickel Strip Thermal Stability and Safety
Nickel exhibits excellent thermal stability, which is paramount for maintaining battery performance and safety. Its ability to withstand elevated temperatures without compromising structural integrity reduces the risk of thermal runaway, a phenomenon associated with overheating in batteries. So, this means that nickel can get really, really hot before it melts. This property ensures the reliability and safety of battery packs, particularly during demanding operating conditions.
Nickel Corrosion Resistance and Longevity
Unlike copper, nickel is known to be essentially corrosion-proof. In fact, one of nickel's most significant properties is its exceptional resistance to corrosion. This resistance minimizes degradation and ensures prolonged battery life, making nickel an attractive choice for manufacturers aiming to deliver reliable and long-lasting energy storage solutions.
It’s important to consider, however, that the series conductor is generally not exposed in a battery pack. This is because battery packs are usually wrapped with several layers of tape and PVC. Air can still get in there, though, so having a material that doesn’t corrode is still important for the longest possible longevity. This is even more true if you live near the ocean or in some other highly salty environment.
Mechanical Properties and Structural Integrity of Nickel Strip
Nickel possesses favorable mechanical properties, including high tensile strength and excellent ductility, which contribute to the structural integrity of battery packs. These properties are particularly crucial in applications where batteries may undergo mechanical stress or vibrations, such as in e-bike batteries. This is important for batteries in high-vibration environments. In these situations, nickel's mechanical resilience ensures the reliability and performance of battery packs under varying conditions.
In contrast, copper is a very soft and highly pliable material. So, even though copper is a much better conductor than nickel, using copper will cause your battery pack to miss out on the added structural integrity provided by nickel.
Nickels Compatibility and Enhanced Performance
Nickel's compatibility with other battery materials enhances its suitability for battery pack construction. When combined inside the cell with elements like lithium, cobalt, and nickel forms cathode materials with high energy density, enabling greater storage capacity within limited space. Outside of the battery, nickel can easily be soldered or welded without having to worry about how the nickel is going to react to the process. This compatibility results in more powerful batteries that are easier to build than they would be if another material was used.
Economic Viability of Nickel
From an economic standpoint, nickel's abundance and relatively low cost compared to alternative materials make it economically viable for large-scale battery production. Its widespread availability ensures a stable supply chain, mitigating concerns related to material scarcity or price volatility. This economic advantage further reinforces nickel's role as a preferred material in battery pack construction.
So, if you are still wondering why you use nickel strips for battery packs, it’s due to their exceptional thermal stability, corrosion resistance, mechanical strength, and low cost. The ability of nickel strips to withstand high temperatures enhances safety by minimizing the risk of thermal runaway. The corrosion resistance of nickel strips helps ensure longevity, particularly in salty environments. Nickel's mechanical properties contribute to the structural integrity of battery packs, making them reliable under various heavy-duty conditions.
Using Nickel With Copper
Integrating copper into battery pack construction alongside nickel can indeed offer a "best of both worlds" approach, leveraging the superior conductivity of copper while still benefiting from the structural integrity and other advantageous properties of nickel. This method often involves a technique known as the "copper-nickel sandwich."
Copper is well-known for its exceptional conductivity, far surpassing that of nickel. By incorporating copper into the battery pack design, manufacturers can enhance the overall efficiency of energy transfer within the cells, thus improving performance.
The copper-nickel sandwich technique typically involves spot welding a layer of nickel on top of a layer of copper, creating a composite strip that combines the strengths of both materials. This secondary weld bonds the copper layer to the cell, ensuring reliable electrical connectivity while still benefiting from the thermal stability, corrosion resistance, and mechanical resilience of nickel.
This approach allows you to optimize the design of battery packs, balancing electrical conductivity with structural integrity and safety considerations. By strategically incorporating copper-nickel sandwiches into the construction of battery packs, manufacturers or DIYers can achieve enhanced performance and longevity while maintaining cost-effectiveness.
We hope this article informed you on exactly why nickel strips are used for battery packs. Thanks for reading!