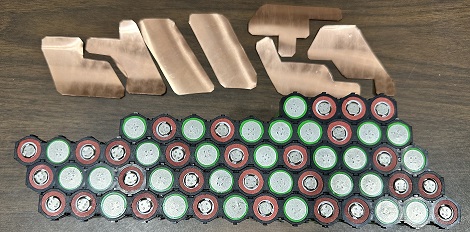
Can You Spot Weld Copper?
Table of Contents
Yes, copper can be indirectly spot-welded by using a nickel weld as a catalyst.
Copper is harder to weld than nickel because it has a low electrical resistance. This lower resistance produces less of a voltage drop and therefore less heat. With the right tools and methods, however, copper can be indirectly spot-welded.
Why is Copper Difficult To Spot Weld?
Copper, being an extremely low-resistance metal, can handle much more current than nickel. Due to its low resistance, it takes a lot of current to spot-weld copper directly. Due to its low resistance, it also makes it ideal to build a battery out of copper. Copper is so good at handling current that it can handle the welding current and won't melt.
Nickel: A Catalyst for Spot Welding Copper
Given copper's inability to directly support spot welding, nickel comes into play as a catalyst to indirectly spot weld copper. When a nickel weld is performed near copper with sufficient power, the heat generated is enough to melt not only the nickel but also the copper on the other side. This process allows a bond to form throughout both metals. This technique is commonly called a copper-nickel sandwich.
Despite the challenges involved, spot welding copper has several advantages. Copper has a vastly superior conductivity compared to nickel, which results in a more efficient transfer of energy. This is why high-performance battery systems always use copper.
What Is The Best Copper For Spot Welding?
When it comes to copper thickness, 0.1-millimeter thick copper is best suited for spot welding. It is also possible to spot-weld 0.15-millimeter thick copper, but this requires highly advanced welders, robust power supplies, and a lot of experience in how to spot-weld. With standard equipment, even something as efficient as a K weld, difficulties arise when attempting to weld 0.15 copper. Using 0.2-millimeter copper is completely out of the question due to its thickness.
[[ aff type=aff ~ link=https://amzn.to/3o3UKRb ~ title=`Copper Sheet .1mm` ~ image=https://admin.cellsaviors.com/storage/copper-foil-.1mm.jpg ~ description=`Best copper sheet to use for doing copper/nickel sandwich. Can be cut easily with scissors. ` ~ height=small ~ buttonText=`Check Price` ]]
What is The Thickest Copper You Can Spot Weld?
When it comes to spot welding copper, the thickness of the material plays a crucial role in the success of the operation. The maximum thickness that can be effectively spot welded using a kWeld, one of the best spot welders, is typically around 0.15 millimeters. However, achieving this thickness requires optimal conditions, including a high-quality bench power supply and extremely sharp welding probes.
The power supply must be capable of delivering the amps required for spot welding copper that thick, which is a highly conductive material. The sharpness of the probes is also critical, as it ensures the current is concentrated at the spot of the weld, enabling the welding of thicker materials.
In more realistic conditions, the maximum thickness for spot welding copper is usually around 0.1 millimeters. This is due to the challenges presented by the high thermal and electrical conductivity of copper. Despite these limitations, there are techniques to work around this issue. One such method involves layering, where multiple welds are performed one on top of the other.
This technique allows for the creation of series connections with metals that are traditionally too thick to be spot welded. While the thickness of the material that can be welded in a single operation is limited, performing multiple welds can theoretically overcome these limitations. This opens up possibilities for using a wider range of materials, including thicker copper, when it comes to building lithium battery packs.
Safety Precautions in Spot Welding Copper
When spot welding copper, it’s crucial to take several safety precautions due to the unique challenges this metal presents. The high temperatures produced during the process generate significantly more fumes and smoke than nickel welding, which can be harmful if inhaled. In addition to dealing with the safety concerns of spot-welding copper, you should also be following the best safety practices with lithium-ion batteries.
Ventilation: Ensure you have adequate ventilation in your workspace to avoid exposure to these harmful fumes and gasses. Treat copper welding the same way you would soldering in terms of ventilation. An extraction fan or a fume extraction system can be beneficial in maintaining a safe environment.
Power Source Safety: Copper welding requires a high amount of electrical energy. Make sure your power source is capable of handling the load without risk of overheating or short-circuiting. Regularly inspect your power source for any signs of damage or wear.
Heat Management: The welding probes can become extremely hot during the process. Either wear heat-resistant gloves to protect your hands or wrap your welding probes with some sort of thermally insulative material.
So Why Batteries Spot-welded With Nickel Over Copper?
Batteries are made with nickel because it is easier to spot weld and has excellent anti-corrosive properties. These two factors make it the go conductor used when building battery packs. Nickel is nowhere near the ideal material for battery production. It has a much higher resistance than copper, aluminum, or even brass. This means that for the same amount of current, nickel will always run hotter and be less efficient.
Spot welding operates by channeling a high amount of power through a small area. For materials like nickel that have a high resistance, this produces a very large voltage drop that results in a large amount of power dissipated into the weld area as heat.
This heat is intense enough to be able to liquefy several layers of metal. This intense heat, however, is highly localized and doesn’t make its way into the cell chemistry.